Rene Joppi, Commercial Director at Mackwell discusses the challenges we face and opportunities that lie ahead.
Since the tragic events of June 2017, which saw 72 people lose their lives in the fire that engulfed Grenfell Tower in West London, the area surrounding building safety and compliance is now, more than ever before, at the forefront of people’s minds.
Although not defined as a public or commercial premise, the 24 storey residential tower block contained many communal areas such as escape routes, assembly points and walkways which would have required a building risk assessment to help ensure the safety of the occupants and minimize the risk of fire. Amongst other things, the risk assessment would have defined the need for evacuation aids such as the provision of a fire prevention system, sprinkler system and emergency lighting.
In 2005, engineering consultancy, Capita Symonds compiled a report into the tower which contained a number of health and safety concerns regarding the emergency lighting system installed throughout the building. The report stated that the emergency lighting had fallen below standard and that the system was not being properly managed by the appointed responsible person, and that there was a perceived unwillingness to acknowledge the need for urgent maintenance and repair.
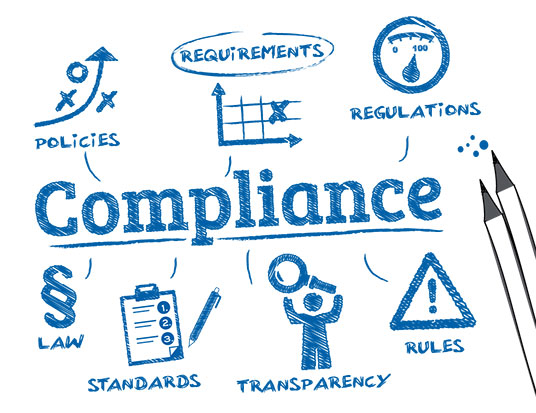
The report stated that the emergency lighting had fallen below standard and that the system was not being properly managed by the appointed responsible person, and that there was a perceived unwillingness to acknowledge the need for urgent maintenance and repair.
The report went on to specifically highlight the essential requirement for adequate emergency lighting to ensure the safe and immediate evacuation of occupants in an emergency situation, due to a lack of natural daylight in the building’s stairwells. Furthermore, the report stated that the building’s occupants were constantly at risk because of the ‘non-functioning emergency lighting’.
Grenfell Tower is just one example of a residential building where the emergency lighting of communal areas was deemed as inadequate, yet in this area, it is unfortunately not alone, and this continues to be the case. As recently as 2018, a survey revealed that more than 40% of residential housing estates have the same issue of sub-standard and inadequate emergency lighting systems. This 40% figure however, is only representative from actual buildings surveyed and found to have to have non-compliances. In reality the figure is much higher and is estimated to be closer to 80%.
Compliance and emergency lighting
There are a number of health and safety and construction directives together with legislative material which is published to ensure the health and safety of building occupants. In the area of fire safety, the government’s fire regulatory reform order applies, and it is this order that specifies the need for the initial risk assessment.
The risk assessment
Before embarking on the design, a full risk assessment must be undertaken to determine the areas in the building which have a requirement for emergency lighting. This will include escape routes, open areas, points of emphasis such as locations of essential fire safety equipment and any areas deemed as high-risk task. Communal areas within residential properties may only form perhaps 10% of the core area but must still be covered by a full risk assessment, carried out by a qualified, responsible person.
Lux levels and signage
An accurate and compliant emergency lighting scheme design, undertaken in line with the initial risk assessment, and the emergency lighting code of practice, BS 5266-1 and its accompanying standards; BS EN 50172 and EN 1838, will ensure that the areas covered are illuminated correctly and adequately. In many cases however, the risk assessment is not adhered to correctly, partly due to budgetary constraints and unhelpful timescales etc. As a result, the lighting levels can be compromised as lower quality, inferior fixtures are used and the number of fixtures as specified is reduced. This can lead to poor uniformity and ‘dark spots. Similarly, a poorly designed escape route with poor quality or incorrect exit signage can lead to confusion and ambiguity in an emergency escape period.
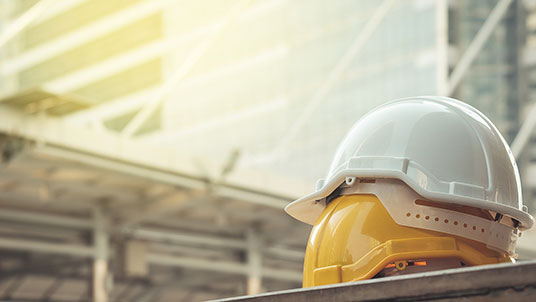
Component abuse and end of life failure
A scheme designed and installed in line with the risk assessment and the relevant emergency lighting standards will ensure initial compliance. This, however, is just the start. For the emergency lighting to remain compliant throughout its designed lifetime, there are many factors to be considered. The performance of its associated components is heavily dependent on how they are operated and maintained. The rechargeable battery for instance is a critical component but it can be highly susceptible to abuse through neglect, exposure to high temperatures and over-cycling etc. For self-contained emergency lighting applications, the battery must satisfy a four-year design life in line with BS EN 60598-2-22. It is often the case though that the battery has seen many full cycles in a very short period of time due to mains interruptions and power outages associated with ‘pre-handover’ installation periods. In many cases, the battery is connected and installed sometimes weeks or months before the mains power is applied. In these critical periods the battery may discharge to dangerous levels from which it cannot recover. Some control gears use remote software commands such as inhibition mode and rest mode to prevent unnecessary battery discharge, but this is generally in conjunction with a control system. The battery has a maximum ambient temperature rating of 50⁰C but often this figure is exceeded as the battery is placed in thermally unsuitable luminaires during the re-engineering process. Exposure to temperatures above the battery’s maximum rating can impact greatly on the lifetime.
Another consideration is the maintenance of the emergency lighting fixture. For instance, if placed in a dirty environment, the light source may not be delivering its declared luminous flux, resulting in lower levels of illumination.
Intelligent diagnostics and compliance
Taking into account the requirements and challenges mentioned above, it is easy to see how difficult it can become for the appointed ‘responsible person’ to maintain the compliance of the emergency lighting scheme. Upkeep of the logbook, including logging any changes to building layout, structure and the internal fabric. Reparations, changes to the décor, colour schemes, all have an impact on the on-going compliance of the scheme. Monitoring the health of the battery and control gear manually, without an automatic test system renders the task almost a full-time role.
To take the battery as an example, it is almost impossible to monitor its health whilst ensuring it still operates within its designed parameters throughout its life. Some manufacturers have now started to develop diagnostics through on-board software to monitor battery health.
Diagnostics allow the user to interrogate several parameters from the emergency lighting control gear, as it logs and records through its lifetime. The idea is to provide the responsible person with preventative data regarding the on-going performance of the associated equipment and to highlight any potential problems or drop in performance.
One example of diagnostic data collection is the ability for the control gear to monitor and record its own temperature for retrospective and on-going analysis. This can then be used to help maintenance of the battery for instance, as it approaches end of life, rather than after end of life failure.
Additionally, and perhaps more significantly, diagnostics can be used to monitor and record the number and frequency of emergency switching cycles. From this it can be interpreted whether the components are being operated correctly within their designed parameters.
Diagnostics can be used to measure and record the battery voltage, again providing valuable preventative information on battery health and status.
These are just some of the benefits that intelligent emergency control gears can offer through their diagnostic functionality. As developments expand, many more values can be recorded and used to aid more efficient, preventative maintenance and thereby ensure the scheme remains compliant and effective, whilst keeping tighter control of the costs associated with reactive maintenance.
In a rapidly changing world where technology is evolving on a daily base and impacting on our personal lives, it is logical to presume that more intelligent technologies will find their way into public buildings as well.
Diagnostics, if used correctly and as intended will help to ensure that safety critical systems, such as fire prevention and emergency lighting, benefit in terms of compliance and efficiency whilst helping to keep occupants safe.
The Capita Symonds report highlighted the lack of a compliant emergency lighting system in Grenfell tower in 2005. Whether this situation remained in place up to and during the tragic events of June 2017 is not clear, but what is certain is that a non-compliant emergency lighting system could only have added to the general feeling of panic and disorientation. In short, it would have served as a hindrance rather than help. If we have the opportunity to help maintain the on-going compliance of these buildings and the safety of their occupants, by producing intelligent technologies, we should take it. These are just some of the benefits that intelligent emergency control gears can offer through their diagnostic functionality. As developments expand, many more values can be recorded and used to aid more efficient, preventative maintenance and thereby ensure the scheme remains compliant and effective, whilst keeping tighter control of the costs associated with reactive maintenance.
Further information is available from Mackwell on 01922 742145 by email [email protected] or by visiting the company’s website at www.mackwell.com